Blog
Breaking the Mold with Additive Manufacturing
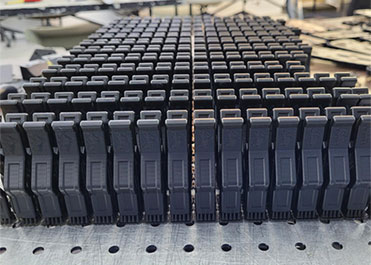
Written by Trenton Willson
In a former career, I was a Production Manager at Baer Bronze – A Fine Art Foundry. This was by far one of the neatest jobs I have had because of how interesting the whole process was. Now, as a writer for Merit3D, I see parallels to the bronze casting process and in the mass production of plastic parts and products.
Injection molding has been the means of producing plastic parts for a very long time. The process is fairly simple but at the same time has some very significant bottlenecks or cost issues in an ever-changing market.
Additive manufacturing or 3D printing is a fairly new technology and is proving its superiority in many ways. I will highlight 4 in this article.
Overhead costs – In conducting a simple Google search, the cost of purchasing an injection molding machine could cost anywhere from $25-80K and depending on the size, complexity, and capacity, the cost could be much more. Injection molding machines are also very complex, requiring a great deal of maintenance, fluids, electricity, and monitoring only adding to the cost. In comparison, an industrial 3D printer costs $3-12K per unit and can produce similar quantities with less residual costs to operate and maintain the machine. These 3D printers also require less manual input and monitoring which saves a significant amount of labor costs.
Due to the cost-effectiveness of a 3D printer, it also makes it easier for companies to produce parts in-house eliminating the shipping costs of purchasing from an overseas producer.
Warehousing/Inventory – One of the biggest developments in manufacturing in the Western Hemisphere over the last few decades is the understanding of just-in-time inventory versus the overproducing of products to carry inventory. In college, one of my textbooks was the business novel, “The Goal,” by Eliyahu M. Goldratt. This book has become the standard by which manufacturing companies operate. The book describes the theory of constraints and addresses the issues of working through bottlenecks. Alex Rogo is the main character in the story. He is a struggling plant manager who is on the verge of losing his job because of the failing level of production of his operation. He is re-connected with a former Physics teacher that helps him see how excess inventory and bottlenecks in his organization are stifling his efficiency. As Alex figures these things out, his plant begins to improve, and ultimately the entire plant is saved.
The storage of inventory and the cost to maintain it can literally sink a company into ruin. Unfortunately, in the world of manufacturing, there is the juggle between bulk purchases of inventory to drive the price down and ordering what you need which is the most effective and least risky. Additionally, shipping is one of the greatest bottlenecks in the world of manufacturing and creating the parts in-house or closer to home reduces the risk of delayed shipments.
Additive manufacturing, because of its efficiency and cost-effectiveness, opens up the proverbial door of near-perfect just-in-time manufacturing. Parts can be produced locally, or even in-house in half the time and at half the cost.
Flexibility in product changes – When I worked at the fine art foundry, I learned a great deal about the process of taking an original work (prototype), usually sculpted in clay, to a finished bronze sculpture. The original sculptures (prototype) would be used to make a mold made by painting silicon rubber onto the surface several layers thick. Once the silicone was dried, a plaster cast was applied to the outside of it to give the silicone the rigidity needed to hold its shape. Larger sculptures were sectioned and made into smaller molds that fit together later for the larger sculpture. Smaller ones could be done with a single mold.
Once the mold was made, hot wax was poured into the mold. Only small sculptures were made as solid bronze. Most others were just the outer shell. Once the wax had been poured several layers thick it was removed from the mold. The mold lines were cleaned off and sprues were added to the wax. Sprues are basically a series of channels or pipes where the bronze will flow to fill the cavity of the sculpture. Once the wax replica is ready, it is run through a series of dips into a slurry mixture which creates a porcelain cast on the outside of the wax replica. When the proper thickness of slurry is dried the cast is placed in a furnace that quickly melts the wax out of the cast leaving a clean space for the bronze to be poured. The bronze is then heated to a molten consistency and poured into the cast. The bronze is cooled and the cast is broken off. The sculpture is then taken to the metal shop where a metal chaser cleans any flaws, and if it is a larger sculpture, welds the pieces together.
Now, can you imagine if the artist were to come with a slight change to their original? This process from mold to finish can take up to several weeks and it has to start with the mold. In 3D printing, it is merely a change in the programming to adjust the design and the print is ready. No new prototype is needed, no mold is necessary to change the old version to a new one.
A new product can completely avert the entire process. It is as if the welder creates the entire sculpture in his shop with the efficiency and accuracy of a machine. That is pretty amazing!
No waste – In the case of the bronze foundry, suppose that the artist says, this new sculpture is the only one you can sell from now on. If there were several castings of the original, those would no longer be available and all costs that went into making them would be lost. Fortunately, bronze is easily re-melted down and used in other sculptures. With injection molded parts, often you cannot repurpose the plastic, and shipping it back to the manufacturer is not a cost-effective option. Plastic may be recycled, but rarely can it be reused by the same person.
Obsolescence and breakage are reduced dramatically when the parts are printed as needed locally or in-house. It makes a great deal of a difference.
My manager at the foundry was a very detail-oriented man who had the bronze casting process to a science. He was very efficient and had created a process that reduced waste and got the casting right the first time more than any other foundry in the area. The process, known as the “Lost Wax Method” has been around since ancient Egypt and though it is tried and true, it can be a lot of work to change the art even if the changes are slight. Additive manufacturing, or 3D printing is changing the production process around the world by simplifying how prototypes are developed electronically to an almost perfect state and printed in a very short timeframe. Merit3D is proud to be a pioneer in this transition that brings your manufactured parts closer to home, and made in the USA.